Cold-forged products are items created through the processing of metal materials using the cold forging process. Cold forging is a method of shaping metal materials at room temperature or relatively low temperatures under pressure. This process provides high precision, strength, and durability, making it widely utilized across various industries. Additionally, cold forging dies are advantageous as they are used under conditions below the tempering temperature of steel, resulting in minimal impact on their lifespan due to heat.
Business Overview
A comprehensive support system revolving around plastic processing, with a focus on the fabrication of molds for cold forging.
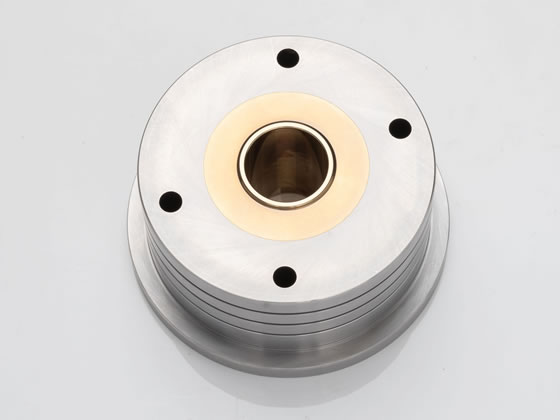
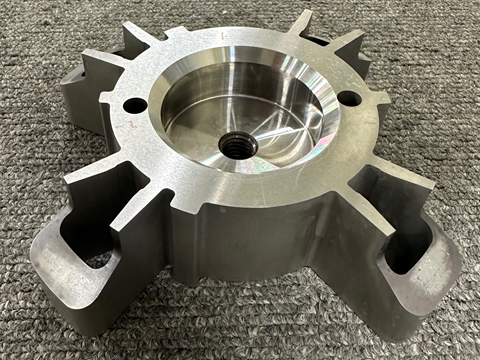
Precision Press Die Manufacturing
Precise press dies are a type of mold used for the high-precision extrusion, cutting, and bending processes of metal sheets or strip materials. They are crucial for manufacturing products that require dimensional accuracy and find application in various manufacturing processes such as electronic devices, automotive components, medical equipment, aerospace parts, and more.
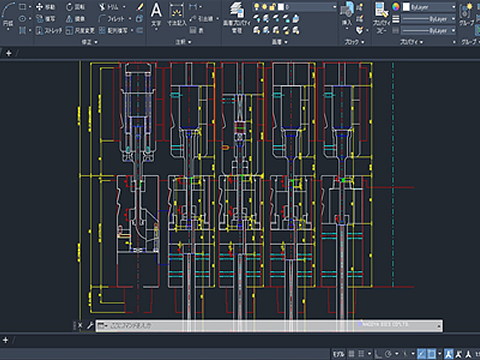
Cold Forged Product Die Design
The design of molds for cold-forged products requires advanced technical skills and specialized knowledge, as it has a significant impact on the quality and performance of the final products. The design process typically begins with defining the requirements of the product, followed by creating a detailed 3D model of the mold, including its specific shapes and dimensions. Additionally, the fabrication of mold components involves heat treatment to achieve the necessary hardness and wear resistance. This step plays a crucial role in determining the lifespan and performance of the mold.
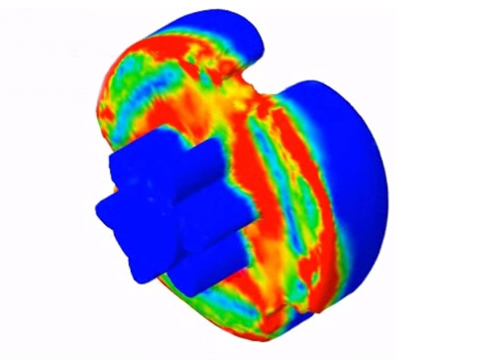
Cold Forging and Mold Simulation
The molds undergo rigorous testing in actual processes against stringent criteria. Depending on the results, adjustments may be made, including confirming durability and modifying internal and external shapes of the mold as necessary. Once the design is verified to function correctly, the process moves on to full-scale manufacturing.
The three techniques advocated by Nagoya Dies
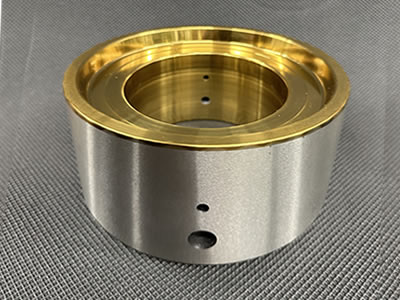
Technology (High Durability/Lifespan)
In pursuit of reducing mold costs for products, our cold forging dies (quenching and tempering dies) with a history of over 30 years offer high durability, contributing to cost savings for our customers and ensuring high productivity.
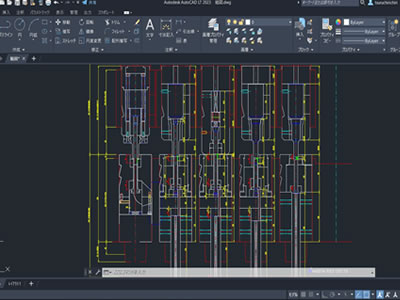
High Quality (Proposal-oriented)
We are advancing towards becoming a proposal-oriented company, assisting and proposing solutions for our customers in the design and fabrication of dies for cold forging hammers, headers, press dies for cold forging, and other general press dies. We address daily user demands and offer proposals based on Nagoya Die's extensive experience and accumulated data.
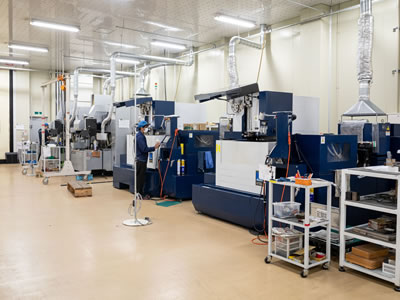
Workflow (High Precision)
Anticipating the future with precision, our high-precision molds are manufactured in a temperature-controlled facility at 20°±1°, equipped with numerous high-precision machining tools and measuring instruments.
Example of Workflow
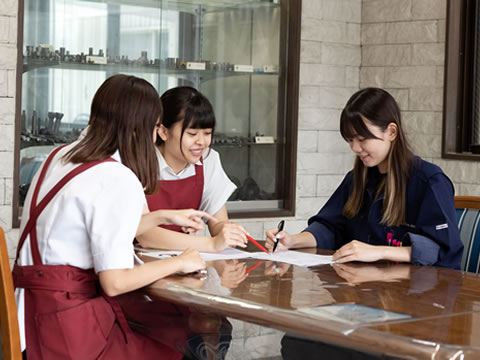
Consultation and Meetings
We aim for a net shape.
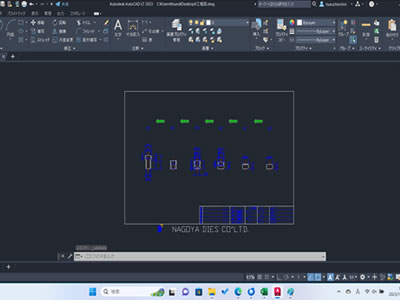
Mold Design
Utilizing extensive experience and accumulated data, we calculate processing rates and loads, determining process distribution.
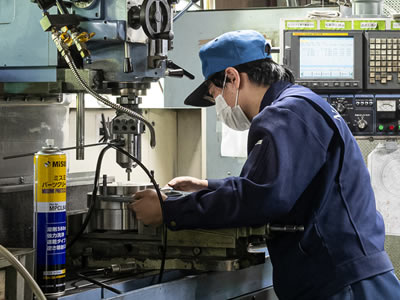
Mold Manufacturing
By manufacturing in-house at our own facility, we have achieved mold production that fully incorporates the distinctive features of process design.
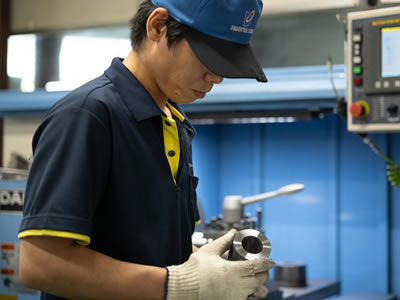
Prototype Production
For checking challenging processes, we conduct prototypes and shape verification using our 300-ton hydraulic press. Additionally, upon request, our designers can travel to the user's facility to oversee prototype trials.
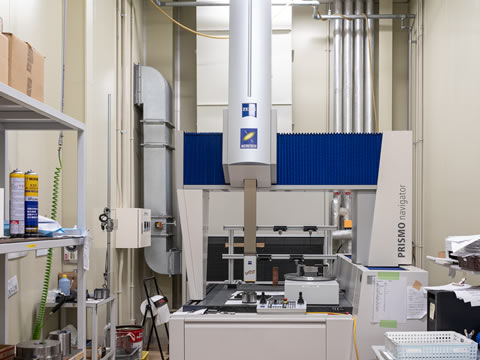
Quality Inspection
We conduct measurements to meticulously inspect the finished product.
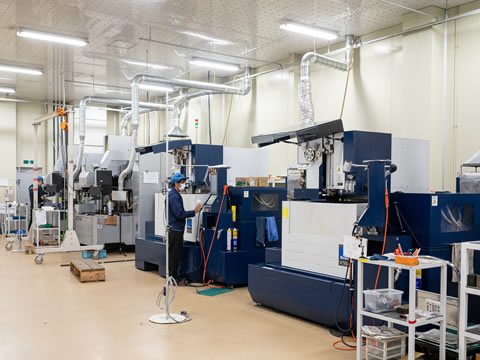
Mass Production
We will continue to assist with aspects such as lifespan improvement even after the start of mass production.